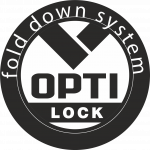
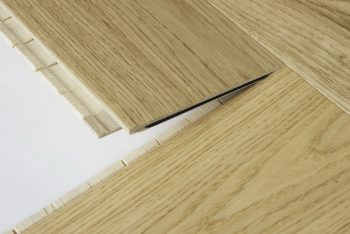
Modern Classic Herringbone Joint
CLASSIC HERRINGBONE FLOATING INSTALLATION
The New Optilock™ joint enables installation without the need for RIGHT AND LEFT-HAND BOARDS.*This is Barlinek’s new glueless front joint to make installation of Classic Herringbone boards CLEAN, QUICK AND EASY.
*See the installation instructions and warranty card for detailed information on the installation and use of the Classic Herringbone boards.
OPTILOCK ENSURES: :
- Compared to the instalation of a classic herringbone with right and left-handed boards, there is half of the material waste
- Twice as fast installation
- Saves time during purchase
- No need to calculate right and left-hand boards
- You can do it yourself which means simple, inexpensive and fast installation.
- Can be laid on old floorboards and non-renovated floors.
- The floor is ready for use immediately after installation.
- Damaged boards can be easily replaced.
- Can be laid on underfloor heating
- Our joint can withstand the pressure of a 65 mm roller with a force of 6,000 N, which is a load of over 600 kg
INSTALLATION VIDEO
Floating installation
Glue down installation